Per abilitare questa innovazione che aumenta la flessibilità, Rockwell Automation ha collaborato con Analog Devices e ha utilizzato la sua tecnologia di controllo
Rockwell Automation: mette in moto la trasformazione digitale.
In risposta all’aumento dei costi dell’energia, alle tensioni geopolitiche e alle persistenti interruzioni della supply chain, gli operatori industriali stanno ora dando priorità agli investimenti che garantiscano resilienza, flessibilità e sostenibilità alle proprie attività.
Il sistema di trasporto intelligente MagneMover® LITE è la risposta smart di Rockwell Automation a questo ambiente sfidante in cui i produttori si vedono costretti a operare.
MagneMover LITE è un sistema di trasporto intelligente che offre un concetto modulare flessibile, in cui ciascun modulo è costituito da una sezione di motore lineare che si adatta a formare una varietà quasi infinita di configurazioni per affrontare qualsiasi esigenza industriale.
Supera i trasportatori a nastro e a catena tradizionali per le applicazioni OEM/in-machine e per i requisiti di movimentazione più impegnativi, offrendo nuovi livelli di ottimizzazione dei processi e di produttività. Infatti, rispetto a un sistema di trasporto tradizionale, Rockwell afferma che il MagneMover LITE possa aiutare i produttori ad aumentare i tempi di operatività di 10 volte, a risparmiare fino al 25% sul costo dell’energia e a risparmiare fino al 25%-30% sul tracciato dell’impianto, a seconda dell’applicazione.
Per abilitare questa innovazione che aumenta la flessibilità, Rockwell Automation ha collaborato con Analog Devices e ha utilizzato la sua tecnologia di controllo del movimento Trinamic®, che include la soluzione TMC2130A, per implementare appieno la funzionalità di motion control di MagneMover LITE.
La precisione e le capacità diagnostiche di questa soluzione hanno permesso a Rockwell Automation di fornire tutta l’architettura e le funzionalità necessarie in MagneMover LITE. Il risultato è un sistema che sta aprendo nuove porte alla necessità, da parte dei produttori, di avere un’operatività più flessibile ed efficiente dal punto di vista energetico.
In sintesi
Azienda
Rockwell Automation è leader mondiale nell’automazione industriale e nella trasformazione digitale, che unisce l’immaginazione delle persone al potenziale della tecnologia, per espandere ciò che è umanamente possibile e rendere il mondo più produttivo e sostenibile. Con sede centrale a Milwaukee, nel Wisconsin, Rockwell Automation ha una forza operativa di circa 28.000 persone che risolvono problemi e si dedicano ai propri clienti in oltre 100 Paesi del mondo.
Obiettivo
Consentire ai clienti di raggiungere i propri obiettivi operativi e di produttività, permettendo loro di spostare carichi leggeri in modo rapido ed efficiente.
Sfida
Implementare completamente le funzionalità di controllo del movimento di MagneMover LITE e fornire la prossima generazione di operazioni di automazione industriale efficienti. Per ADI ciò ha significato fornire un circuito integrato con la precisione e le capacità diagnostiche necessarie affinché MagneMover LITE funzionasse come da specifiche.
Soluzione ADI
Soluzione integrata TMC2130A – con capacità diagnostiche per adattare in modo intelligente le prestazioni in uso e la flessibilità di controllare due motori con un unico circuito integrato – che si integra perfettamente nella funzionalità di controllo del movimento di MagneMover LITE.
Rockwell Automation magnemover lite
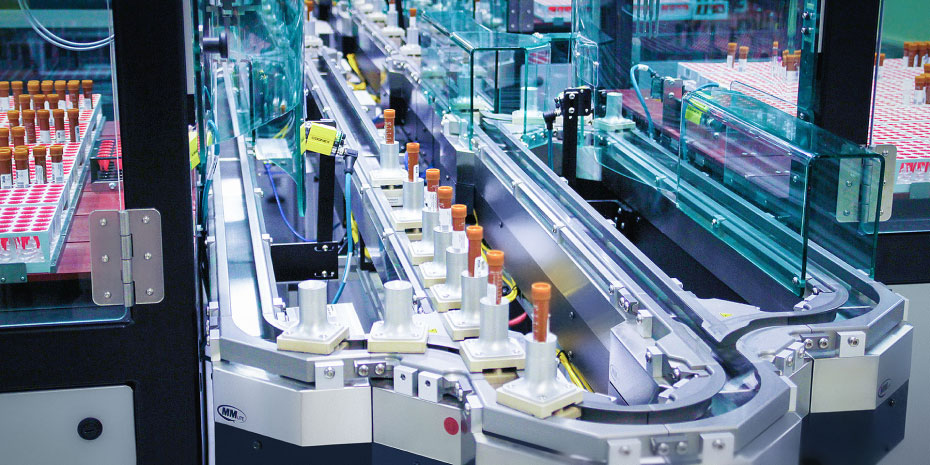
Movimento intelligente
Posizionamento accurato (non sono necessari fermi meccanici), movimento bidirezionale, movimento fluido, tracciamento continuo del carrello e reportistica.
Ottimizzazione del processo
Gli strumenti di simulazione e configurazione semplificano la progettazione e l’ottimizzazione del sistema.
Tracciabilità completa
Identificazione univoca di ciascun carrello e della sua posizione in ogni momento, con una reportistica completa per la tracciabilità dei dati e la possibilità di assegnare priorità all’instradamento dei singoli trasportatori.
Layout flessibili
I layout del sistema possono essere orientati in diversi modi, per adattarsi allo spazio.
Adatto a molteplici applicazioni
Applicabile alla produzione farmaceutica, al riempimento sterile e asettico, al confezionamento di alimenti e bevande, all’automazione di laboratorio, all’immagazzinamento, al settore automobilistico, ai dispositivi medici e alla produzione di prodotti di consumo.
Facile da pulire e manutenere
Lavabile con un grado di protezione IP65. Poche parti mobili significano meno manutenzione.
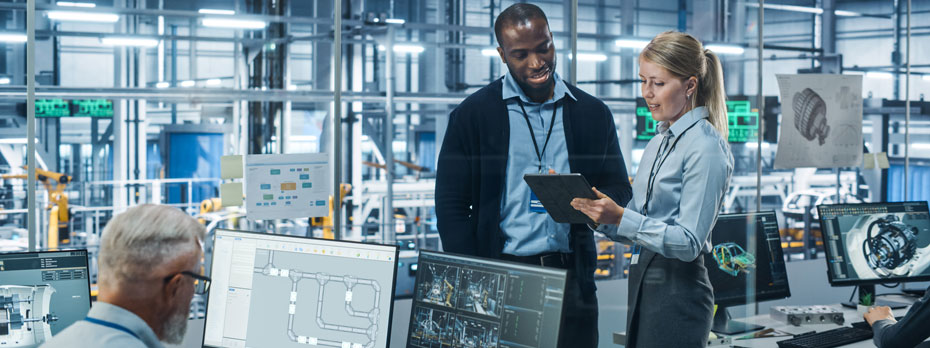
“Rockwell sapeva di dover collaborare con un’azienda dotata di una tecnologia di controllo del movimento all’avanguardia e ADI era la scelta perfetta. Grazie all’utilizzo della tecnologia di Motion Control Trinamic di ADI, il sistema MagneMover Lite di Rockwell è in grado di funzionare con precisione e flessibilità, esattamente come previsto”.
Anuj Mahendru, Global Industry Director, Semiconductor and High Tech, Rockwell Automation
Il controllo di movimento Trinamic di ADI porta Rockwell Automation a un livello di efficienza piú elevato
La realizzazione di questa soluzione richiede un controllo del movimento di precisione per lo spostamento bidirezionale, l’arresto e l’avvio intelligente dei carrelli dei materiali, la sincronizzazione del movimento con gli altri macchinari presenti nello stabilimento e una risposta dei motori di trazione che si adatti in modo efficiente alle dimensioni del carico. Rockwell Automation ha collaborato con Analog Devices e la sua tecnologia di controllo del movimento Trinamic per creare un altro livello di efficienza nell’automazione industriale. Il TMC2130A è un driver ad alte prestazioni per motori stepper bifase e include due funzionalità molto interessanti:
StealthChop™ Voltage Chopper
Il sofisticato StealthChop Voltage Chopper di Trinamic garantisce un funzionamento praticamente silenzioso, combinato ad una maggiore efficienza e ad una coppia del motore migliorata.
Tecnologia CoolStep™
CoolStep di Trinamic è un controllo di corrente sensorless, dipendente dal carico, che aziona i motori alla potenza minima necessaria per le condizioni di carico effettive, riducendo il consumo energetico dei motori stessi e la generazione di calore – parametri critici per migliorare l’efficienza e adattare le prestazioni a esigenze mutevoli.
Implementando queste funzionalità nel sistema MagneMover LITE, Rockwell Automation sapeva che avrebbe avuto a disposizione la tecnologia per fornire un sistema AHMS ad alta efficienza energetica, in grado di effettuare un Motion Control di precisione, richiesto dai produttori alla ricerca di una flessibilità sempre maggiore.
ADI ha apprezzato così tanto il magnemover lite che lo sta utilizzando anche internamente
ADI è rimasta talmente colpita dalla funzionalità di MagneMover LITE che lo sta implementando nei propri stabilimenti di Beaverton, Oregon e Limerick, Irlanda.
Rockwell Automation distribuirà negli stabilimenti ADI oltre 2 km di binari MagneMover LITE, utilizzabili per il trasporto e l’immagazzinamento, che consentiranno a ADI di ridurre lo spazio utilizzato, una caratteristica preziosa per le operazioni di fabbrica.
Nel complesso, questo sistema modulare di nuova generazione di Rockwell Automation può offrire vantaggi fondamentali a ADI, che lo ha scelto perché può contribuire a:
- Ridurre il trasporto interno
- Creare efficienza nella movimentazione dei materiali
- Consentire l’implementazione del sistema in aree precedentemente impossibili
- Scalare l’implementazione di pari passo con la crescita della fabbrica.
Inoltre, prima ancora di installare un solo pezzo di binario, Rockwell Automation e ADI hanno creato insieme un modello digitale di come l’AHMS si integrerebbe nella fabbrica.
Questo ha permesso a ADI di avere una prospettiva unica su come l’AMHS di Rockwell Automation si collegherebbe a tutti i sistemi di programmazione, spedizione e MES di ADI, il tutto prima che iniziasse l’installazione, dando a ADI delle informazioni uniche su come le prestazioni di precisione dell’AMHS migliorerebbero la produttività e gli utili futuri.
“Prevediamo che l’implementazione della tecnologia dei carrelli indipendenti nei nostri stabilimenti migliorerà la produttività degli operatori di quasi il 20%. La tecnologia MagneMover consentirà agli operatori di concentrarsi su altre attività invece di consegnare manualmente i lotti attraverso la fabbrica. Si tratta di un enorme guadagno di produttività!”.
José J. García, Managing Director, Wafer Fab Sustainability and Autonomous Enterprise, Analog Devices
Con Rockwell Automation magnemover lite si è “sul binario giusto” verso una produzione efficiente
In generale, Rockwell Automation e ADI hanno obiettivi di trasformazione manifatturiera/digitale, molto simili: migliorare la qualità della vita rendendo il mondo più produttivo e sostenibile con la prossima generazione di produzione intelligente. Questa relazione reciprocamente vantaggiosa con queste soluzioni tecnologiche all’avanguardia – il MagneMover LITE di Rockwell Automation e il Trinamic Motion Control di ADI – è la dimostrazione che due grandi aziende possono collaborare e offrire processi di produzione più efficienti, che migliorano la produttività e riducono al minimo l’impatto ambientale.
Analog Devices ti aspetta a SPS Norimberga 2024 per trasformare il futuro del settore industriale presso il Padiglione 5, Stand 110.